Designing parts for injection molding requires careful consideration of various factors to ensure successful production outcomes. From optimizing part geometry to minimizing manufacturing defects, several key design principles can significantly impact the quality and efficiency of the injection molding process. In this blog, we’ll explore some essential tips for designing parts that are optimized for injection molding.
- Incorporate Draft Angles: Draft angles are critical for facilitating the ejection of molded parts from the mold cavity. Without draft angles, the part may become trapped in the mold, leading to production delays and potential damage to the part or mold. Incorporating draft angles—typically 1 to 2 degrees per side—allows for smooth ejection and prevents surface imperfections such as drag marks and scratches.
- Maintain Uniform Wall Thickness: Maintaining uniform wall thickness is essential for achieving consistent part quality and minimizing warping and sink marks. Variations in wall thickness can result in uneven cooling rates, leading to internal stresses and dimensional inaccuracies in the finished part. Designing parts with uniform wall thicknesses—typically between 2 to 4 millimeters—helps ensure proper material flow, efficient cooling, and structural integrity.
- Avoid Sharp Corners and Thin Features: Sharp corners and thin features can pose challenges during the injection molding process, increasing the risk of part defects such as sink marks, voids, and stress concentrations. To mitigate these issues, it’s advisable to design parts with rounded corners and filleted edges. Additionally, avoid incorporating thin sections or features that may be prone to warping or distortion under the pressure and heat of the molding process.
- Design for Moldability: Consideration of moldability is crucial when designing parts for injection molding. Design features such as undercuts, overhangs, and complex geometries can complicate the mold design and increase production costs. By designing parts with simplicity and manufacturability in mind, you can streamline the molding process and minimize the risk of tooling issues and production delays.
- Pay Attention to Gate Placement: Gate placement plays a significant role in determining the flow of molten material into the mold cavity and influencing part quality. Ideally, gates should be positioned in areas of the part that minimize aesthetic impact and allow for uniform filling and packing of the cavity. Common gate types include edge gates, sprue gates, and pin gates, each offering distinct advantages depending on the part geometry and material properties.
- Consider Material Selection: Selecting the appropriate material is critical for achieving desired performance characteristics and meeting application requirements. Factors to consider when choosing a material include mechanical properties, chemical resistance, temperature stability, and cost. Work closely with material suppliers and injection molding experts to identify the most suitable material for your specific application needs.
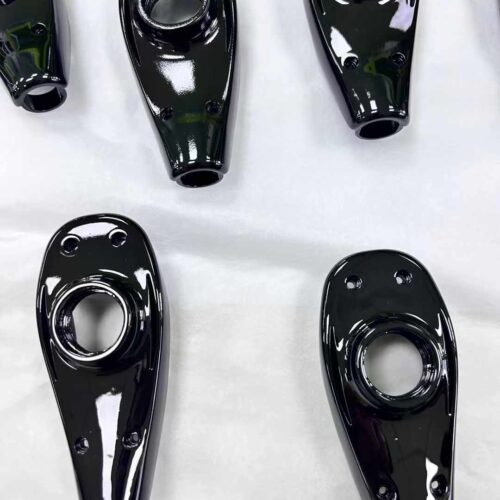
Conclusion: By following these design tips, you can optimize your parts for successful injection molding, minimizing defects, reducing production costs, and ensuring high-quality outcomes. Collaboration between designers, engineers, and injection molding professionals is essential for achieving optimal results and unlocking the full potential of injection molding technology. With careful consideration of design principles and thorough validation through prototyping and testing, you can bring your vision to life with confidence and precision.